Innowacje oparte na technologiach cyfrowych stają się obecnie kluczowym rozwiązaniem służącym wzmacnianiu konkurencyjności przedsiębiorstw różnych branż. Wśród technologii o przełomowym znaczeniu w tym kontekście coraz częściej wymienia się technologię cyfrowego bliźniaka (Digital Twin), która bazuje na systemach cyberfizycznych (Cyberphysical Systems), Internecie Rzeczy (IoT) i Przemysłowym Internecie Rzeczy (IIoT) [2]. Do niedawna technologia ta wykorzystywana była niemal wyłącznie w przemyśle kosmicznym i lotniczym – do monitorowania stanu maszyn, oceny ich zużycia oraz przewidywania awarii i usterek całych systemów konstrukcyjnych bądź ich części. Jednak dzięki zwiększającej się skali wykorzystania czujników oraz urządzeń połączonych i komunikujących się ze sobą za pomocą Internetu rośnie zainteresowanie wykorzystaniem cyfrowych bliźniaków również w innych obszarach i sektorach gospodarki [1, 3].
Wskazuje się, że cyfrowy bliźniak mógłby istotnie usprawniać i optymalizować procesy biznesowe i procesy produkcji również w przedsiębiorstwach przemysłu spożywczego [1, 3]. W 2019 roku firma Gartner szacowała, że do 2021 r. połowa dużych firm przemysłowych na świecie stosować będzie cyfrowe bliźniaki, co przełoży się na wzrost ich wydajności o 10% [3]. Wiele przedsiębiorstw przemysłu spożywczego stoi obecnie przed trudnym zadaniem wypracowania optymalnej ścieżki rozwoju, uwzględniającej nowe wyzwania oraz nowe szanse związane z pogłębiającymi się procesami cyfryzacji. Wybór rozwiązań i technologii cyfrowych gwarantujących przedsiębiorstwom przemysłu spożywczego możliwie najwyższy zwrot z inwestycji nie jest jednak oczywisty. Pojawiają się bowiem pytania i wątpliwości, czy przedsiębiorstwa przemysłu spożywczego powinny decydować się na wdrażanie najbardziej zaawansowanych technologii cyfrowych, które wykorzystywane były dotąd niemal wyłącznie w sektorze hi-tech do poprawy zarządzania cyklem życia złożonych produktów. Analiza potencjalnych korzyści oraz kosztów związanych ze stosowaniem poszczególnych technologii cyfrowych okazuje się więc szczególnie istotna w przypadku przedsiębiorstw tego sektora. Technologia cyfrowego bliźniaka jest jedną z najbardziej złożonych i równocześnie najmniej rozumianych technologii cyfrowych. Pomimo że wykorzystuje stosowane od dawna rozwiązania (m.in. wspomagane komputerowo
STRESZCZENIE: |
Szybki rozwój systemów cyberfizycznych, Internetu Rzeczy i innych technologii cyfrowych istotnie zwiększył możliwości tworzenia wirtualnych replik wielu obiektów fizycznych. Wśród potencjalnych obszarów zastosowań wirtualnych modeli wymienić należy cyfrowe bliźniaki całych zakładów, procesów produkcji, produktów spożywczych i opakowań. Ogólne szacunki wskazują, że wykorzystanie technologii cyfrowych bliźniaków może przełożyć się na 10-procentowy wzrost wydajności przedsiębiorstwa. Technologia cyfrowych bliźniaków jest jedną z najbardziej złożonych i wymagających technologii cyfrowych. Dodatkowo wciąż znajduje się na wczesnym etapie rozwoju, co może utrudniać wdrożenia oraz zwiększać ryzyko ich niepowodzenia. Przedsiębiorstwa w pełni zautomatyzowane, gdzie produkcja może być sterowana i optymalizowana zdalnie za pomocą cyfrowych kopii produktów, procesów i linii produkcyjnych, zyskują znaczne przewagi konkurencyjne. Olbrzymie znaczenie technologii i rozwiązań cyfrowych uwidacznia również obecny kryzys związany z globalną epidemią choroby COVID-19. Przedsiębiorstwa scyfryzowane w mniejszym stopniu odczuwają negatywne skutki obostrzeń, które wprowadzane są w odpowiedzi na nowe rodzaje zagrożeń epidemicznych. |
SUMMARY: |
The rapid development of cyber-physical systems, the Internet of Things and other digital technologies has greatly increased the possibilities for creating virtual replicas of many physical objects. Potential application areas include digital twins for entire factories, production processes, food products and packaging. General estimates indicate that the use of digital twin technology can translate into a 10% increase in enterprise efficiency. Digital twin technology is by far one of the most complex and demanding digital technologies. In addition, it is still at an early stage of development, which may hinder implementation projects and increase the risk of failure. Fully automated enterprises, where all production can be controlled and optimized remotely using digital copies of products, processes and production lines, acquire significant competitive advantages. Also, the current crisis associated with the global epidemic of COVID-19 highlights the enormous importance of digital technologies and digital solutions. Digitized enterprises are less affected by the negative effects of restrictions that are being introduced as a response to new types of epidemic threats. TITLE: Digital Twin Technology in The Food Industry Enterprises – Requirements, Potential Applications, Limitations |
projektowanie 3D), wiedza na jej temat jest wciąż ograniczona. Warto zatem przybliżyć możliwości zastosowania tej technologii w przedsiębiorstwach przemysłu spożywczego. W artykule zaprezentowano koncepcję cyfrowego bliźniaka, schemat działania, funkcje i usługi technologii, wymogi związane z jej wdrożeniem oraz potencjalne obszary zastosowań i ograniczenia cyfrowych bliźniaków w przedsiębiorstwach przemysłu spożywczego.
DEFINICJE I ROZUMIENIE cyfrowego bliźniaka
Cyfrowy bliźniak opisywany bywa najczęściej jako model złożony z jednostki fizycznej, wirtualnego odpowiednika jednostki fizycznej oraz połączeń zapewniających przepływ danych między nimi [6]. Obliczenia i symulacje opierające się na złożonych algorytmach oraz nieprzerwanym i dwustronnym przepływie danych między jednostką fizyczną a jednostką wirtualną dostarczają informacji, wskazówek i wiedzy, które służą poprawie cech i wydajności jednostek fizycznych [14]. W prasie specjalistycznej i literaturze można znaleźć wiele definicji oraz ujęć koncepcji cyfrowych bliźniaków [10]. Częściowo wielość definicji wynika stąd, iż cyfrowy bliźniak nie jest całkowicie nowym rozwiązaniem. Wywodzi się bowiem z takich koncepcji i rozwiązań, jak modelowanie trójwymiarowe, symulacje i prognozowanie czasu zdatności maszyn do eksploatacji, wirtualne systemy produkcji czy cyfrowe prototypowanie.
Koncepcję cyfrowego bliźniaka szerszemu gronu przedstawił po raz pierwszy Michael Grieves w trakcie konferencji poświęconej zarządzaniu cyklem życia produktu (Product Lifecycle Management) w Michigan w 2003 roku. Grieves wskazywał, że łączność między jednostkami fizycznymi w przestrzeni realnej i jednostkami wirtualnymi w przestrzeni wirtualnej oraz powiązane z nimi przepływy danych dają ogromne możliwości w obszarze monitorowania, zarządzania i ulepszania produktów w ciągu całego cyklu ich życia [11]. Kilka lat później, dzięki pracom inżynierów NASA, koncepcja cyfrowego bliźniaka zaczęła nabierać realnych kształtów. Tworzone za pomocą technologii symulacje pracy silników pojazdów kosmicznych pozwalały m.in. analizować stan ich żywotności, przewidywać przebieg awarii czy przenoszenie się pęknięć zmęczeniowych. Obecnie najczęściej przytaczana definicja cyfrowego bliźniaka bazuje na definicji NASA z 2010 roku. Zgodnie z nią „cyfrowy bliźniak jest zintegrowaną wielofizyczną, wieloskalowalną i probabilistyczną symulacją złożonego produktu, która wykorzystuje najlepsze dostępne modele fizyczne, aktualne dane z czujników etc., by odzwierciedlać życie swojego bliźniaczego odpowiednika” [15]. W kolejnych latach zainteresowanie cyfrowym bliźniakiem istotnie wzrosło, głównie w związku z dążeniem największych przedsiębiorstw do realizacji idei i założeń Przemysłu 4.0. W 2016 roku firma Siemens jako pierwsza pokazała możliwości wykorzystania tej technologii w szerszym kontekście przemysłowym. Opracowane pakiety oprogramowania oraz modele komputerowe umożliwiały projektowanie, kontrolowanie oraz optymalizowanie części, produktów, procesów produkcyjnych, usług bądź całych zakładów produkcyjnych w świecie wirtualnym [4].
Najnowsza definicja cyfrowego bliźniaka zaprezentowana w Encyklopedii Inżynierii Produkcji CIRP wskazuje, że cyfrowym bliźniakiem jest „cyfrowa reprezentacja działającego unikalnego produktu (rzeczywistego urządzenia, obiektu, maszyny, usługi lub aktywu niematerialnego) lub unikalnego systemu produktowo-usługowego (systemu składającego się z produktu oraz powiązanej usługi), która za pomocą modeli, informacji i danych odzwierciedla jego wybrane cechy, właściwości, stan i zachowania w ramach jednej lub wielu faz cyklu jego życia” [10]. Przytoczona definicja uwzględnia ostatnie zmiany w rozumieniu koncepcji cyfrowego bliźniaka – przejście od wirtualnych replik dotyczących wyłącznie produktów fizycznych do replik uwzględniających również mniej materialne jednostki, takie jak organizacja procesów produkcji czy powiązane z produktami usługi [2, 15].
SCHEMAT DZIAŁANIA I USŁUGI cyfrowego bliźniaka
Podstawą działania cyfrowego bliźniaka jest współpraca i integracja między przestrzenią fizyczną a przestrzenią wirtualną. Główną siłą napędową cyfrowego bliźniaka są jednak dane. Cyfrowy bliźniak gromadzi i wykorzytuje dane wieloczasowe, wielowymiarowe, wieloźródłowe i heterogeniczne [12]. Dane generowane przez jednostki fizyczne obejmują dane statyczne i atrybutowe informujące np. o rozmieszczeniu jednostek w przestrzeni oraz dane dynamiczne informujące o aktualnej pracy jednostki. Dane generują również jednostki wirtualne, w tym modele symulacyjne. Istotnym źródłem danych dla cyfrowego bliźniaka są równocześnie usługi przez niego świadczone (m.in. symulacje, monitoring, prognozowanie) [2]. Cyfrowy bliźniak uwzględnia dodatkowo dane zewnętrzne stanowiące sumę wiedzy ekspertów dziedzinowych oraz wiedzy pochodzącej z innych źródeł. Jak wskazują Qi i wsp. [12], niektóre dane mają charakter danych fuzyjnych – powstają w wyniku połączenia wszystkich wskazanych kategorii danych. Centrum danych zasila wszystkie elementy składowe cyfrowego bliźniaka – modele obiektów i modele scenariuszy, usługi, produkcję oraz projekty produktów i obiektów. Połączenia w cyfrowym bliźniaku zapewniają też równoległy przepływ danych ze wskazanych elementów do centrum danych (rysunek 1).
Rozwiązania określane mianem cyfrowego bliźniaka mogą być stosowane w całym cyklu życia produktu – od etapu początkowego związanego z planowaniem produkcji w zakładzie i projektowaniem produktu po kolejne etapy związane z zaopatrzeniem i przygotowaniem materiałów do produkcji, przetwarzaniem materiałów i pakowaniem produktów aż do etapów związanych z dystrybucją produktów oraz ich użytkowaniem przez odbiorców końcowych [11]. Tworzone modele pozwalają monitorować stan obiektów fizycznych (produktów, linii produkcyjnych i procesów), przeprowadzać symulacje ich zachowań oraz wykrywać usterki i awarie, zanim te pojawią się w przestrzeni fizycznej. Bez tworzenia kosztownych fizycznych prototypów możliwa staje się również ocena funkcjonalności i jakości projektowanych produktów, w tym ocena przygotowania linii produkcyjnej do uruchomienia produkcji. Dzięki modelom zawierającym reguły działania odwzorowywanych obiektów cyfrowy bliźniak może samodzielnie wykonywać czynności logiczne – przeprowadzać analizy i dokonywać ocen, a następnie na ich podstawie autonomicznie podejmować decyzje, w tym proponować działania naprawcze, uruchamiać procesy i jednostki fizyczne czy uzupełniać modele wirtualne służące do kolejnych symulacji [12]. Można wyróżnić sześć podstawowych usług świadczonych przez cyfrowego bliźniaka, są nimi [12]:
- monitorowanie stanu obiektów i procesów (produktów, maszyn, linii produkcyjnych),
- symulacja funkcji produktów, w tym wydajności poszczególnych elementów projektowanych produktów,
- symulacja rozwoju produktów i obiektów,
- dynamiczne planowanie produkcji,
- konserwacja predykcyjna,
- kontrola jakości produktów i procesów produkcji.
W rezultacie cyfrowy bliźniak zapewnia optymalizację jednostek i procesów w przedsiębiorstwie – pozwala zwiększać wydajność, utrzymywać bezpieczeństwo procesów oraz podnosić jakość produktów. Optymalizację uznać można za główną i docelową funkcję cyfrowego bliźniaka.
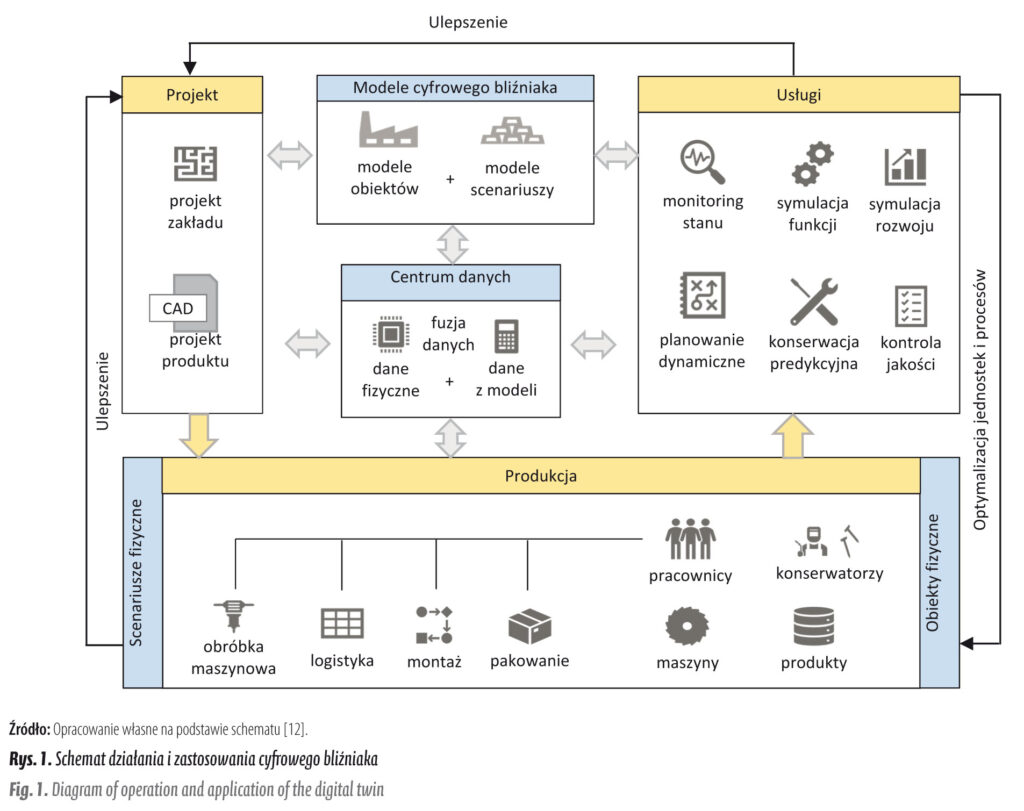
WYMOGI ZWIĄZANE Z WDROŻENIEM cyfrowego bliźniaka
Wdrożenie cyfrowego bliźniaka jest złożonym, wymagającym i czasochłonnym procesem [7]. Cyfrowy bliźniak opiera się bowiem na wielu zaawansowanych technologiach i rozwiązaniach, które dopiero razem zastosowane pozwalają na realizację wszystkich jego funkcji. Jego wdrożenie rozważać mogą przedsiębiorstwa, które posiadają zautomatyzowane linie produkcyjne oraz systemy cyberfizyczne takie jak: roboty, programowalne sterowniki logiczne i inne elementy niezbędne do kontroli ruchu maszyn i obrazowania. Nieodzowne dla działania cyfrowego bliźniaka są równocześnie technologie i urządzenia, które zapewniają łączność i niezakłóconą komunikację między obiektami fizycznymi i wirtualnymi, oraz technologie i programy pozwalające na gromadzenie i przetwarzanie przyrastających zasobów danych, w tym na prowadzenie zaawansowanych analiz i symulacji w czasie rzeczywistym. Biorąc pod uwagę wskazane potrzeby, do technologii i rozwiązań kluczowych dla właściwego działania cyfrowego bliźniaka w przedsiębiorstwie zaliczyć należy [10, 12]:
- technologie bezprzewodowej komunikacji, w tym technologię 5G, Internet Rzeczy, Przemysłowy
- Internet Rzeczy,
- czujniki (w tym RFID) rejestrujące dane,
- Ethernet umożliwiający komunikowanie się urządzeń w sieci lokalnej,
- aktuatory (siłowniki) wprowadzające zmiany w środowisku fizycznym,
- technologię chmury obliczeniowej,
- analitykę dużych zbiorów danych wspieraną przez algorytmy maszynowego uczenia się, algorytmy predykcyjne i sztuczną inteligencję.
Wdrożenie cyfrowego bliźniaka w przedsiębiorstwie wymaga również dostępu do specjalistycznej wiedzy dotyczącej tworzenia i działania modeli symulacyjnych. Cyfrowy bliźniak nie jest zwykłym modelem 3D, wirtualnym odbiciem obiektu fizycznego czy oprogramowaniem do zarządzania cyklem życia produktów (PLM) [7]. Modele wirtualne w cyfrowych bliźniakach muszą być niezwykle wiernym odbiciem obiektu fizycznego. Powinny też charakteryzować się solidnością, wysoką standaryzacją (w zakresie kodowania, interfejsów i protokołów komunikacyjnych) oraz modularyzacją, tj. składać się z modułów, które można od siebie oddzielać, łączyć i ponownie wykorzystywać [12]. Ze względów bezpieczeństwa fundamentalne znaczenie ma także możliwość odtworzenia kolejnych kroków i działań, które doprowadziły do stworzenia modelu. Opracowanie pełnej dokumentacji dla wirtualnych modeli symulacyjnych jest jednym z najważniejszych działań w procesie wdrażania cyfrowego bliźniaka. Umożliwia utrzymanie płynności procesów również w przypadku zmian kadrowych czy zakończenia współpracy z dostawcami zewnętrznymi. Cyfrowy bliźniak wymaga ponadto od przedsiębiorstw nowego podejścia do procesów zarządzania produkcją. Obecnie kontrola procesów produkcji w przedsiębiorstwach zautomatyzowanych opiera się na piramidzie automatyzacji. Produkcja planowana jest na dłuższy okres przez systemy informacyjne przedsiębiorstwa (takie jak ERP), a następnie zaplanowaną sekwencję działań kontroluje się przez systemy realizacji produkcji (MES). Cyfrowy bliźniak wymaga mniej hierarchicznych, za to bardziej elastycznych podejść do kontroli procesów produkcji [2]. Symulacje przeprowadzane w oparciu o dane czasu rzeczywistego mogą wskazywać na lepszą sekwencję działań, a tym samym zmieniać scenariusze produkcji w trakcie jej trwania. Pełne wykorzystanie potencjału cyfrowego bliźniaka wymaga więc włączenia modeli symulacyjnych do systemów kontroli produkcji w przedsiębiorstwie.
MOŻLIWE OBSZARY ZASTOSOWANIA i ograniczenia cyfrowego bliźniaka w przedsiębiorstwach przemysłu spożywczego
Przemysł spożywczy zaliczany jest do sektorów mniej zaawansowanej techniki, w których innowacyjne i złożone rozwiązania technologiczne wykorzystywane są stosunkowo rzadko. Z drugiej strony w ostatnim okresie obserwuje się istotny wzrost tempa automatyzacji i robotyzacji procesów produkcji w przedsiębiorstwach tego sektora – zarówno na poziomie przetwórstwa, jak też na poziomie procesów związanych z sortowaniem, pakowaniem, etykietowaniem i paletyzowaniem produktów żywnościowych. Nowoczesne zakłady wykorzystują roboty również do automatycznej oceny jakości wytworzonych produktów. W 2018 r. liczba nowych instalacji robotów przemysłowych w przedsiębiorstwach przemysłu spożywczego i napojów na świecie zwiększyła się o 32% w porównaniu z rokiem 2017 [8]. W USA sektor spożywczy jest obecnie drugim po sektorze motoryzacyjnym sektorem odnotowującym najwyższe tempo wzrostu zamówień na roboty przemysłowe [13]. Sprzedaż robotów do przedsiębiorstw przemysłu spożywczego rośnie też w Chinach i Europie [8]. Można się spodziewać, że rola automatyzacji i robotyzacji w przemyśle spożywczym będzie rosła w kolejnych latach. Dotyczyć to będzie szczególnie krajów, w których przedsiębiorstwa borykają się z problemem rosnących kosztów pracy i niedoborów siły roboczej [5]. Na przyspieszenie robotyzacji wpływać mogą również podwyższone wymogi w zakresie bezpieczeństwa higienicznego żywności oraz nowe zagrożenia pandemiczne na świecie. Maszyny i zautomatyzowane linie produkcyjne pozwalają na produkcję bezdotykową, równocześnie uniezależniają przedsiębiorstwa od potencjalnych przestojów w produkcji wynikających z chorób pracowników. W przedsiębiorstwach w pełni zautomatyzowanych – posiadających dodatkowo cyfrowe kopie produktów, procesów i linii produkcyjnych – cała produkcja może być sterowana i optymalizowana zdalnie, bez konieczności organizowania pracy na terenie zakładu.
Profity z wdrożenia cyfrowych bliźniaków i innych zaawansowanych technologii mogą jednak różnić się istotnie w poszczególnych branżach przetwórstwa spożywczego. Ten ostatni jest bowiem bardzo niejednorodnym sektorem – każda branża ma swoje specyficzne wymagania i potrzeby. Stosowanie zaawansowanych rozwiązań cyfrowych może być ekonomicznie uzasadnione tylko w określonych obszarach funkcjonowania przedsiębiorstwa bądź tylko dla niektórych rodzajów i typów produkcji. Przykładowo korzyści wynikające z posiadania cyfrowych bliźniaków produktów świeżych, nisko przetworzonych oraz o krótkim terminie przydatności do spożycia będą prawdopodobnie mniejsze niż korzyści wynikające z posiadania cyfrowych bliźniaków produktów trwalszych, wysoko przetworzonych oraz opartych na złożonych recepturach. Dodatkowo zwrot z inwestycji w bardzo kapitałochłonne rozwiązania z zakresu robotyki, sztucznej inteligencji i cyfrowego bliźniaka możliwy jest co do zasady w przypadku zakładów prowadzących produkcję na dużą skalę. Duże i zautomatyzowane przedsiębiorstwa funkcjonują zazwyczaj jako sieć zakładów, które muszą w sposób elastyczny dostosowywać plany produkcji i linie produkcyjne do zmieniających się warunków rynkowych. W opisanych przedsiębiorstwach profity z zastosowania cyfrowego bliźniaka mogą być znaczne – od lepszego planowania produkcji, podniesienia wydajności procesów produkcyjnych i usprawnienia procesów projektowania po wyższą jakość i bezpieczeństwo produktów żywnościowych [1]. Potencjalne obszary zastosowania cyfrowego bliźniaka w przedsiębiorstwach przemysłu spożywczego zaprezentowane zostały na rysunku 2.
Poprawa wydajności procesów i optymalizacja wynikają również z szerszych możliwości współpracy pracowników w przedsiębiorstwach stosujących cyfrowe bliźniaki. Wirtualne modele obiektów umożliwiają bowiem równoległą pracę nad produkcją i projektowanymi zmianami wszystkim zaangażowanym działom i podmiotom, w tym m.in. działowi badań i rozwoju, technologom żywności, działowi planowania produkcji i kosztów, inżynierom linii produkcyjnych, działowi prawnemu czy specjalistom ds. marketingu i sprzedaży. W takich warunkach szybciej i sprawniej można uzupełniać modele o dane istotne dla optymalizowania receptur i produktów pod kątem mocy produkcyjnych i możliwości finansowych przedsiębiorstwa, wymogów rynków lokalnych czy regulacji krajowych i międzynarodowych. W rezultacie cyfrowe bliźniaki pozwalają na obniżenie kosztów innowacji i szybsze wprowadzanie na rynek nowych produktów.
Choć potencjalne korzyści wynikające z wdrożenia cyfrowego bliźniaka w przedsiębiorstwach przemysłu spożywczego są ogromne, ich osiągnięcie może być trudne. Z tego względu przedsiębiorstwa sektora powinny mieć szerszą wizję i strategię wykorzystania nowych technologii cyfrowych do optymalizacji. Istotna przy tym okazuje się również świadomość, że cyfrowy bliźniak jest technologią na wczesnym etapie rozwoju – uzyskanie wiernych replik niektórych obiektów i produktów wciąż bywa bardzo wymagającym i czasochłonnym procesem [7]. Dla przedsiębiorstw sektora dostosowujących się do wyzwań Przemysłu 4.0 kluczowe będzie zatem określenie obszarów, w których tworzenie cyfrowych bliźniaków byłoby zarówno możliwie, jak i opłacalne. Dostępne studia przypadków pokazują, że jednym z pierwszych obszarów, w których z powodzeniem testuje się wykorzystanie danych czasu rzeczywistego z systemów zbliżonych do cyfrowych bliźniaków, jest system kontroli zużycia energii elektrycznej w przedsiębiorstwie [9]. Projekty z tego zakresu mogą istotnie ułatwiać tworzenie modeli wirtualnych różnych scenariuszy procesów produkcji. Stanowiłyby więc właściwy punkt wyjścia dla planowania działań na rzecz optymalizacji i ograniczania kosztów przy pomocy cyfrowych bliźniaków. Kolejne działania mogą dotyczyć testowania zastosowań cyfrowych bliźniaków w przypadku wybranych produktów spożywczych oraz ich opakowań. W tym obszarze przydatne mogą okazać się szczególnie cyfrowe kopie produktów wysoko przetworzonych, wieloskładnikowych oraz takich, które dzięki czujnikom umieszczonym na opakowaniach będą mogły gromadzić i wysyłać dane.
PODSUMOWANIE:
Nowe technologie cyfrowe dają przedsiębiorstwom ogromne szanse na zwiększanie wydajności, produktywności i rentowności. Kluczem do optymalizacji procesów i lepszego wykorzystania zasobów są analizy danych prowadzone w czasie rzeczywistym w sposób zautomatyzowany. Cyfrowe bliźniaki – wirtualne modele wiernie odzwierciedlające rzeczywiste produkty i obiekty fizyczne – istotnie podnoszą wartość i przydatność prowadzonych analiz. Korzyści wynikające z posiadania cyfrowych kopii procesów, linii produkcyjnych i produktów nie ograniczają się jednak tylko do poprawy efektywności operacyjnej. Cyfrowe bliźniaki wzmacniają też potencjał innowacyjny przedsiębiorstwa – ułatwiają rozwój nowych produktów i nowych modeli biznesowych. Cyfrowy bliźniak Z tego względu można oczekiwać, że będzie rosła liczba przedsiębiorstw zainteresowanych wdrażaniem opisywanej technologii. Wydaje się, że również obecny kryzys związany z epidemią choroby COVID-19 będzie skłaniał przedsiębiorstwa do przyspieszenia działań na rzecz cyfrowej transformacji. W przedsiębiorstwach przemysłu spożywczego w ostatnim okresie wyraźnie wzrosło tempo automatyzacji i robotyzacji procesów produkcji, co w istocie otwarło drogę do wykorzystania bardziej złożonych technologii takich jak cyfrowe bliźniaki. Wśród potencjalnych beneficjentów zastosowania cyfrowych bliźniaków w sektorze spożywczym wymienić należy duże i zautomatyzowane przedsiębiorstwa, które dostarczają na rynek wieloskładnikowe i wysoko przetworzone produkty. Wciąż jednak trzeba liczyć się z dużym ryzykiem niepowodzenia projektów zakładających szybkie wdrożenia cyfrowych bliźniaków. Cyfrowy bliźniak jest bowiem technologią, która nadal znajduje się na wczesnym etapie rozwoju w kontekście jej zastosowań w Przemyśle 4.0. Dodatkowo dla jej prawidłowego działania konieczne jest wprowadzenie głębokich zmian w systemach kontroli produkcji i zarządzania przedsiębiorstwem.
Dr K. Kosior – Zakład Ekonomiki Agrobiznesu i Biogospodarki,
Instytut Ekonomiki Rolnictwa i Gospodarki Żywnościowej – Państwowy Instytut Badawczy,
Warszawa
e-mail: katarzyna.kosior@ierigz.waw.pl